محصولات مهندسی شده چوب ال وی ال
معرفی , طراحی , ساخت انواع پروفیل های ماسیو ( lvl wood ) در مجموعه فن و هنر ایران زمین
گروه فن و هنر ایران زمین طراح و سازنده انواع تیرهای چوبی , قطعات ماستیو و تولید انواع زهوار و پروفیل های دقیق چوبی , ساخت حرفه ای انواع درب , سازه های چوبی بزرگ و کوچک
(Laminated veneer lumber ( LVL
محصولات مهندسی شده چوب که انواع مختلف آن در بازار موجود است ، ولی lvl بدلیل کاربری بالا و نیاز به فضای بزرگ و تخصص و تجربه در ایران بصورن ضعیف و گاها اشتباه مرسوم شده است .
طراحی و ساخت انواع تیر و تیرچه چوبی , تیر کاذب و تیر باربر
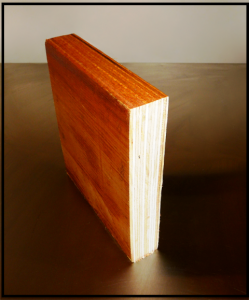
چوب ماسیو چیست؟ ماسیف
بررسی تاثیرات بخاردهی گرده بینه ، خشک کردن لایه ها و فرآیند کهنه سازی، بر روی خواص مکانیکی (LVL)
مشاهده مطالب بیشتر درباره LVL WOOD
سطح مخاطبین این مطلب: کارشناسی ارشد
مولفین :
Forest Industry Engineering Department, Faculty of Forestry Karadeniz Technical University 61080 Trabzon , Turkey
چکیده :
- روکش چوب ، روکش های جالب و زیبا در دکوراسیون منزل
- روکش چوب
- پارکت و کفپوش , انواع چوب و روکش چوب طبیعی در دکوراسیون چوبی
- انواع چوب و روکش چوب طبیعی در دکوراسیون چوبی
در این مطالعه اثرات بخاردهی و شرایط خشک شدن بر روی خواص مکانیکی و دوام LVL والوار چوب ماسیو از طریق مقایسه ای مورد بررسی قرار گرفت . برای این منظور تنه های بخار دهی شده و بخار دهی نشده گونه نوئل و تنه راش بخار دهی شده در دو دمای متفاوت خشک کردن لایه ( º 20 وº110 ) گرفتند. آزمون کهنه سازی برای تعیین دوام LVL و نمونه های چوب ماسیو مطابق با استاندارد EN321 انجام گرفت . عملیات بخار دهی، تمامی خصوصیات مقاومتی بررسی شده را در پانلهای LVL به شکل محسوسی کاهش داد و کمترین میزان تاثیر آن، بر روی مقاومت فشاری بود .
مقدار مقاومت فشاری و همچنین مقاومت به خمش استاتیک در پانلهای LVL راش و نوئل ، از گروه چوبهای ماسیو بدست آمده از همان گرده بینه ها بیشتر بود؛ برخلاف مقاومت به خمش استاتیک و مقاومت فشاری ، مقادیر مقاومت به ضربه پانلهای LVL از نمونه های چوب ماسیو کهنه سازی و بخار دهی نشده کمتر بود .
واژگان کلیدی : بخاردهی تنه ، خشک کردن لایه ،آزمون کهنه سازی ، نوئل اسپراس / راش، LVL خواص مکانیکی
رئوس مطالب مقاله :
1- مقدمه
2- مواد و روشها
3- نتایج وبحث
4- استنتاج
سپاسگذاری ها
منابع ومآخذ
1- مقدمه :
تخته الوار بس لا یا همان LVL” ” یک محصول مهندسی شده چوب است متشکل از لایه های خشک شده حاصل از لوله بری که به صورت موازی الیاف روی هم قرار گرفته اند و توسط یک چسب ضد آب تحت فشار و حرارت تولید می شوند . با این روش از طریق پراکندن معایب بیولوزیک در بین لایه ها با برش دادن تنه های درجه پایین ، محصولی مقاوم از تنه های درجه پایین می توان تولید کرد.
یکی از مهمترین مزایای تکنیکی LVL، نحوه اجرای ویژه آن، ترکیب شدن عملیات تولید و طراحی و محو شدن عیوب بزرگ به دلیل طبیعت خاص فرایند تولید آنهاست. عیوب بزرگی مثل گره ها وسایر خصوصیات کاهنده مقاومت محو شده و یا در تمامی سطح عرضی پراکنده می شوند تا محصول یکنواخت تری تولید گردد ، (2)و(3) .
به سبب یکنواختی خصوصیات ، مقاومت بالاتر و دستیابی واقعی به طول و ابعاد نامحدود، LVL در انواع محصولات از قبیل موارد ذکر شده در زیر استفاده می گردد :
وسایل واجزائ ساختمان و سازه ای ، ساختمانهای چوبی , کلبه , پل سازی , تیرهای مورد مصرف در کف سازی ، در گاراژ ها ، بالای در و پنجره، تیرهای عرضی طاق، الوار داربست وزبانه های پیش ساخته برای انواع اتصالات چوبی تیرهای I و تیرهای لبه دار(HIP).
قبل از گسترش یافتن محصولات مهندسی شده چوب ، سازندگان ساختمان بسیار محدود بودند زیرا الوار چوب ماسیو اغلب ثبات ابعادی و یکنواختی مورد نیاز را فاقد بودند . فرایند تولید وساخت LVL یک محصول مقاوم و با دوام را خلق کرد بسیاری از خواسته ها را که به صورت قابل اطمینانی می توانست تامین نماید.
دومین مزیت LVL در فرایند روکش گیری و چسباندن لایه هاست که امکان ساختن تیرهای بزرگ از تنه های کوچک و کم قطر بسیاری از گونه ها را فراهم می کند و به این وسیله از منابع جنگلی استفاده بهینه و کارآمد تری خواهد شد.
به سبب مزایایی که در بالا به آنها اشاره رفت LVL به عنوان یک جایگزین مناسب برای مصارف ساختمانی پیشنهاد می گردد. هرچند که نتایج تحقیقات در مورد دوام آنها با هم در تناقض هستند ( 5 و 4 ) .
گرین و همکاران ( 4 ) خواص خمشی الوار ساختمانی را بعد از بار گذاری طویل المدت را در دمای º 65 و رطوبت نسبی 75% بررسی کردند ؛ نتایج این بررسی نشان داد که برای 2 تا 3 سال در شرایط دما و رطوبت فوق در اطاق مشروط سازی، مقاومت خمشی LVL نیز مثل الوار چوب ماسیو نوئل / کاج و الوار فییر کاهش می یابد ؛ ولی مقاومت خمشی LVL بعد از گذشت 3 سال سریع تر از الوار چوب ماسیو کاهش یافت.
خصوصیات فیزیکی ومکانیکی LVL ساخته شده از چوب (Rubber wood ) توسط کامالا و همکاران با چوب تیک مقایسه گردید و اظهار شد که LVL رابر وود در بسیاری از خصوصیات با تیک قابل مقایسه بوده و دارای مقاومتی معادل با گاماری ، پون ، گوچ و بنیتیک ، که به عنوان قاب در و پنجره و کف پوش سازی وسایل نقلیه بکار می روند ؛ بود.
بررسی نشان داد که دوام ، خواص مکانیکی و کارکردهای مهندسی LVL متاثر از عوامل بسیاری از جمله گونه چوبی ، ضخامت و کیفیت لایه ها ، متغیرهای شرایط فراوری ،اندازه عضو ، شرایط سرویس و محیط ودر نهایت نوع بارگذاری است .
به عنوان نمونه بخاردهی اولین متغیر در فرایند تولید است ؛ اغلب گونه ها برای لوله بری به بخار دهی نیاز دارند و این کار اثرات منفی بر روی خصوصیات مکانیکی چوب دارد. الوار برخی گونه ها نیز ( نظیر راش ) هم به صورت بخار دهی شده وهم به صورت هوا خشک مورد استفاده قرار می گیرند.
استفاده بهینه و کارامد از LVL در مصارف ساختمانی نیازمند داشتن شناخت و درک از رفتار ساختاری بسیاری از گونه ها و آگاهی از تاثیرات فرایند پیش تیمار کردن تنه ها بر روی خواص مکانیکی و دوام LVL می باشد. بنابراین هدف و مقصود این مطالعه مطرح کردن و پیش رفتن درباره تاثیرات بخار دهی و شرایط خشک کردن بر روی خواص مکانیکی و دوام LVL و الوار چوب ماسیو از طریق مقایسه این دو بوده است.
1. مواد و روشها
برای این مطالعه ، تنه های راش ( Fagus Orientalis ) بخاردهی شده به قطر cm 45 و طولcm 260 از ناحیه ای در نزدیکی مرز ترکیه و گرجستان و تنه های نوئل ( Spruce ) بخار دهی شده و بخاردهی نشده به قطر cm 40 و طولcm 260 از منطقه ترابوزان در شمال ترکیه که هر دو منطقه از نواحی گرمسیری به شمار می روند تهیه گردید .
دو تنه راش و یک تنه از نوئل که دارای رطوبت اولیه 70% بودند، به ترتیب به مدت 12 و 20 ساعت بخاردهی شدند؛ میانگین دمای مغز تنه های راش و نوئل در طی فرایند روکش گیری به ترتیب º 50 وº32 بود. برای رسیدن به شش تنه هر تنه به دو قطعه مساوی به طول cm 65 تقسیم شد یک بخش از هر تنه ( مجموعا سه عدد از آنها ) برای تولید روکش استفاده شدند؛ و سه تنه دیگر برای تولید نمونه های چوب ماسیو استفاده شدند. تنها قسمت برون چوب تنه ها برای آزمایش مورد استفاده قرار گرفت ؛ در پروسه لوله بری فاصله افقی ( فاصله نوک لبه فشار از سطح زیرین تیغه 85% ضخامت روکش ) و فاصله عمودی mm 0.5 بود.
ضخامت روکشهای حاصل از فرایند لوله بری mm2 و ابعاد لایه های حاصله cm 55 * cm 55 بود. سپس لایه های راش از رطوبت اولیه 40% – 50% در خشک کن با دمای º 110 به مدت 5 دقیقه به رطوبت 7% رسیدند.
روکشهای بدست آمده از تنه های بخاردهی نشده حاوی 50% – 60% رطوبت بودند در دمای º 20 برای مدت دو هفته خشک شدند و همراه با روکشهای بدست آمده از تنه های بخار دهی شده و خشک شده در دمای º110 به مدت 5 دقیقه صفحات LVL به ضخامت mm 16 را تشکیل دادند. تولید پانلها سه مرتبه تکرار شد در حدود gr/cm² 180 مخلوط چسب فنل فرمالدهید که حاوی 47% ماده خشک بود بر روی یک طرف لایه ها اعمال گردید .
دما، فشار و زمان پرس داغ به ترتیب º 140 ،N/mm² 1.4 برای راش و N/mm² 0.8 برای نوئل و زمان دوره پرس هم 10 دقیقه بود. دسته جات آزمایش شده در جدول شماره1 نشان داده شده است.
جدول 1 : گروه های آزمونی
راش |
نوئل |
||||
Steamed |
Non-steamed |
Steamed |
|||
Drying temperature |
20 °C |
110 °C |
20 °C |
20 °C |
110 °C |
Solid wood groups |
BW |
— |
SW1 |
SW2 |
— |
LVL panel groups |
— |
B- LVL |
LVL1 |
LVL2 |
LVL3 |
تمامی نمونه های آزمونی تهیه شده برای مقاومت خمش استاتیک ، فشار موازی الیاف و مقامت به ضربه در دو گروه کلاسه بندی گردیده، نمونه های گروه اول در شرایط رطوبت 65% و دمای º 20 مشروط سازی شده تا به تعادل برسند و سپس آزمایش شدند. نمونه های آزمایشی گروههای دیگر تحت فرایند کهنه سازی (Aging) در سه مرحله که در استانداردٍٍٍٍٍٍٍٍEN321 برای تعیین دوام این مواد تعریف شده قرار گرفتند مراحل این سیکل عبارتند از :
1- ماندن در آب با دمای 2± 20برای مدت 1± 72 ساعت
2- انجماد در دمای º 15- برای 24 ساعت
3- خشک شذن در دمای1 ± 70 برای مدت1± 72 ساعت
بعد از انجام این سیکل برای 3 دوره ( 21 روز ) ؛ نمونه های کهنه شده برای مدت 2 ساعت در اتوکلاو با دمای º120 و فشار 1.2 آتمسفر نگهداری شدند، نمونه های آزمایشی در دمای º 20 و رطوبت نسبی 65% مشروط شده و به تعادل رسیدند . تمامی آزمایشات مطابق با استاندارد DIN تعریف شده برای چوب ماسیو صورت گرفت: (52182 DIN) برای دانسیته ،(52185 DIN) برای مقاومت فشاری ،(52186 DIN) برای مقاومت خمشی و در نهایت ( 1-52189 DIN) برای مقاومت به ضربه .
ضخامت نمونه های چوب ماسیو (در جهت شعاعی) برای مقایسه با پانلهای LVL mm16 در نظر گرفته شده بود؛ آزمون مقاومت خمشی بر روی 10 نمونه به ابعاد mm 300*20*16 که از هر پانل بریده شده بود صورت گرفت. برای آزمایش مقاومت فشاری موازی الیاف نمونه هایی با ابعاد mm 30*16*20 مورد استفاده قرار گرفت.
نتایج و بحث
مقادیر دانسیته نمونه های هوا خشک چوب ماسیو و LVL در شکل1 ارائه شده است. براساس آزمایش ،
( دانسیته ) نمونه های چوب ماسیو راش پس از عملیات کهنه سازی تنها 1.5% کاهش یافت دانسیته چوب ماسیو بخار دهی نشده نوئل ( kg/cm³490) در حدود 4.5% از نوئل بخاردهی شده ( kg/cm³469) بیشتر بود و این به ما نشان می دهد که عملیات بخار دهی (بسته به دوره ودمای بخار دهی)موجب این کاهش وزن شده است. (6) هر چند که تنه ها فقط برای 12ساعت بخار دهی شده بودند. میزان کاهش دانسیته نمونه های نوئل بعد از فرایند کهنه سازی قابل اندازه گیری بود.
کاهش دانسیته در نمونه های بخار دهی شده و بخار دهی نشده نوئل به ترتیب 4% و2% بود. گروه LVL راش وهمچنین نوئل مقادیر دانسیته و نیز کاهش دانسیته بیشتری نسبت به چوب ماسیو هریک از LVLهای ساخته شده داشتند. در تولید LVL لایه های به هم چسب خورده تحت فشار پرس می شوند؛ ضخامت صفحات بسته به فشار اعمال شده بر روی چوب کاهش می یابد.
دلیل دانسیته بالاتر LVL به کاهش ضخامت لایه ها در هنگام پرس داغ و نیز دانسیته بالاتر چسب مصرفی در ساخت پانل مرتبط می باشد. علاوه بر آن باید ذکر شود که دانسیته هر دو گروه از چوب ماسیو وLVL پس تسریع فرایند کهنه سازی کاهش یافت.
دلیل کاهش دانسیته، کاهش وزن نمونه ها بود که در هر مرحله از فرایند کهنه سازی اتفاق می افتاد به دلیل اینکه کاهش وزن در اواخر فرایند بخار دهی اتفاق می افتد تغییر قابل ملاحظه ای در دانسیته الوار چوب ماسیو راش مشاهده نگردید. تاثیر فرایند هیدروترمال در بسیاری از مطالعات گزارش شده است (6)، (7) و (8) .
بیشترین کاهش وزن هم در چوب ماسیو نوئل بخار دهی شده و هم نمونه های LVL تعیین شده پس از فرایند کهنه سازی نیز موید این نکته هستند .
شکل 1 – میانگین مقادیر دانسیته نمونه های آزمایش شده ( (n = 30
خواص مکانیکی گروه چوبهای ماسیو راش و LVL قبل و بعد از قرار گرفتن در معرض کهنه سازی تعیین گردید و در جدول شماره 2 ارائه شده است. مقادیر مقاومت خمش استاتیک و مقاومت فشار موازی الیاف گروه چوبهای ماسیو از LVLساخته شده از همان تنه ها کمتر بدست آمد؛ ولی بر خلاف آن مقاومت به ضربه چوب راش به طرز معنی داری بیشتر ازLVL بود و هیچ تغییر معنی داری در مقاومت به خمش استاتیک و مقاومت فشاری موازی الیاف مشاهده نگردید، در حالی که در گروه چوبهای ماسیو بعد از تیمار کهنه سازی ، 33% کاهش در مقاومت به ضربه مشاهده گردید. تیمار کهنه سازی تاثیر قابل ملاحظه ای بر روی مقاومت فشاری موازی الیاف نداشت کاهش مقاومت خمشی بسیار اندک بود و عمده ترین کاهش مقاومت در اثر تیمار کهنه سازی که مشاهده گردید در مقاومت به ضربه ( و در حدود 25% ) بود.
جدول 2 – خصوصیات مکانیکی چوب ماسیو راش و گروه آزمایش شده LVL ، قبل وبعد از تیمار کهنه سازی
Compression strength (N/mm2) |
Bending strength (N/mm2) |
Impact strength (kg m/cm2) |
||||
Control |
Test |
Control |
Test |
Control |
Test |
|
Beech–solid wood |
47.4 |
47.1 |
98.2 |
97.8 |
0.91 |
0.61 |
(1.5)a |
(2.3) |
(5.8) |
(5.1) |
(0.15) |
(0.09) |
|
Beech– LVL |
52.4 |
51.8 |
107.8 |
104.4 |
0.69 |
0.52 |
(1.6) |
(1.8) |
(6.1) |
(4.8) |
(0.03) |
(0.07) |
a Values in parenthesis are standard deviations.
پس از اینکه نمونه های چوب ماسیو بخاردهی شده و نشده نوئل مقایسه شدند ؛ استتنتاج شد که عمل بخار دهی تمامی خصوصیات مکانیکی بررسی شده را به طور قابل ملاحظه ای کاهش می دهد .
کمترین تاثیر بر روی مقاومت فشاری بود و بیشترین خصوصیات مکانیکی متاثر از بخار دهی عبارت بودند از مقاومت خمشی و مقاومت به ضربه .(9) (10) مشابه نتایجی که ما در مطالعه قبلی برای نمونه های آزمایشی با ابعاد سطح مقطع 20*20 یافته بودیم .
(11) مقادیر متوسط مقاومت فشاری نمونه های چوب ماسیو بخار دهی شده از همان مقاومتها در نمونه های بخار دهی نشده ( در حدود 5% ) پایین تر بود.( که در شکل 2 ذکر شده است ) بعد از تسریع کهنه سازی نمونه های چوب ماسیو بخاردهی نشده مقاومت فشاری در راستای طولی الیاف دقیقا 8% کاهش یافت در حالیکه در گروه چوبهای بخاردهی شده تغییر معنی داری مشاهده نگردید.
شکل شماره 2 مقاومت فشاری در جهت موازی الیاف چوب ماسیو وگروه LVL نوئل
در صفحات LVLساخته شده از تنه های یکسان مقاومت فشاری به شکل چشمگیری از چوبهای ماسیو همان گروه بیشتر بود. که در شکل 2 قابل ملاحظه است . فرایند بخار دهی سبب ایجاد تغییرات مشابهی در پانلهای LVL گردید بیشترین مقاومت فشاری در پانلهای LVL نوئل ساخته شده از لایه های حاصل از تنه بخار دهی نشده و هوا خشک در º 20 مشاهده گردید .
در این مطالعه دمای خشک کردن به گونه ای انتخاب شده بود که بر روی مقاومت فشاری پانلهای LVLنوئل تاثیری نداشته باشد؛ که البته در مورد فرایند کهنه سازی این مساله موضوعیت نداشت .
در اثر فرایند کهنه سازی، کاهش مقادیر مقاومتهای فشاری تمام گروه های LVL ، از نمونه های چوب ماسیو بیشتر بود. کمترین مقدار کاهش مقاومت فشاری، در میان گروه های LVL نوئل در پانلهای ساخته شده از لایه های خشک شده در دمای º 110 که از نظر صنعتی یک برنامه خشک کردن ملایم محسوب می گردد؛ مشاهده گردید.
مقدار مقاومت به خمش استاتیک در نمونه های ماسیو بخار دهی شده نوئل 21% کمتر از نمونه های بخار دهی نشده بود ؛ بعد از فرایند کهنه سازی نیز 9% کاهش در مقاومت به خمش استاتیک نمونه های چوب ماسیو بخار دهی نشده نوئل مشاهده و تعیین گردید.
در حالی که تفاوت مشخصی در مقاومت به خمش استاتیک نمونه های بخاردهی شده مشاهده نشد. مقادیر مقاومت به خمش استاتیک گروه های LVL به صورت کاملا مشخصی از گروه چوبهای ماسیو بیشتر و تنها تشابه در مقاومت فشاری بود . در بین گروه های LVL بیشترین مقدار مقاومت خمشی در پانلهای ساخته شده از لایه های هوا خشک حاصل از تنه های بخار دهی نشده اسپراس بود (کنترل N / mm² 98.4 و آزمایش N / mm6 .99 ).
هنگامی که نمونه های LVL2 و LVL3 مقایسه شدند . می توان گفت که دمایی که در این مطالعه برای خشک کردن لایه ها انتخاب شده تاثیر قابل ملاخظه ای بر روی میزان مقاومت خمش استاتیک پانلها نداشته و فرآیند کهنه سازی مقاومت خمشی LVL ها را تحت تاثیر قرار نداد .
شکل 3 مقادیر متوسط مقاومتهای خمشی گروه های چوب ماسیو و LVL
وقتی که مقادیر مقاومتهای فشاری و خمش استاتیک پانلهای LVL هم راش و هم نوئل با گروه چوبهای ماسیو بدست آمده از گرده بینه های یکسان مقایسه شدند، این مقادیر در LVL بالاتر بودند واین موضوع می تواند با شرایط تولید پانلهایLVL مرتبط باشد؛ بر اثر فشار پرس گرم در حین فرآیند تولید ، به صورت متعارف دانسیته پانلها افزایش می یابد و این افزایش دانسیته، به عنوان عامل بهبود دهنده خصوصیات مکانیکی .(مقاومت خمشی در مواد چوبی ) شناخته شده است (12)و(13) به دلیل اینکه پانلهای چوبی موادی چسب خورده هستند، نوع چسب و ضخامت خط چسب همواره بر روی خصوصیات مکانیکی تاثیر مثبتی دارند.
کاهش در مقاومت به ضربه در نمونه های ماسیو نوئل، پس از بخار دهی 21% بود (شکل 4) . مقاومت به ضربه نمونه های چوب ماسیو بخار دهی نشده پس از آزمون کهنه سازی 21% کاهش یافت . مقادیر مقاومت به ضربه پانلهای LVL بر خلاف مقاومت خمشی و فشاری از نمونه های چوب ماسیو که بخار دهی و کهنه سازی روی آنها انجام نشد، کمتر بود .
کمترین میزان مقاومت به ضربه در در گروه LVL3 به دست آمد. کمتر بودن مقاومت به ضربه در پانلهای LVL ممکن است به دلیل شکنندگی الاستیک خط چسب؛ که بعد از واکنش انعقاد صورت می گیرد باشد. یک دلیل کاهش مقاومت به ضربه در پانلهای LVL ممکن است تردی خط چسب باشد .
مقادیر متوسط مقاومت به ضربه چوب نوئل و پانلهای LVL
ممکن است که دلیل کاهش خواص مکانیکی، کاهش و تغییرات شیمیایی در ساختار ماده توسط فرایند هیدروترمال باشد . واضح است که بخار دهی تاثیراتی مثبت بر روی خصوصیات جذب آب ونیز واکشیدگی پانلها می گذارد این تاثیر به هیدرولیز و خروج همی سلولز در طی عمل بخار دهی نسبت داده می شود . (14)
به دلیل اینکه همی سلولز از زنجیزهای سلولی کوتاه و نیز شبکه ای تشکیل شده ، نسبت به دیگر محتویات چوب راحت تر هیدرولیز می گردد. کاهش مقاومتها در اثر تخریب حرارتی به ” اسید اسیتیک مشتق شده از گروه های استیل موجود در ساختار شیمیایی چوب” نسبت داده شده است و فعالیت آن به صورت یک کاتالیزور و باز شتاب دهنده موجب تخریب و کاهش می شود. پهن برگان گروه های استیل بیشتری نسبت به سوزنی برگان دارند.
اسیدهای رزینی تولید شده در طی فرایندهای حرارتی در برخی سوزنی برگان، نیز منشا مهم حساسیت به گرما بیان شده اند.(4) چگونگی فرایند کهنه سازی بر روی خواص مکانیکی نمونه های بخار دهی نشده ای که بررسی شد، تاثیر معنی داری که ممکن است به دلیل محو شدن (خروج) اسیدهای رزینی در طی فرایند بخار دهی باشد . بخار دهی می تواند سبب از دست رفتن (کاهش) ساختار چوب شود ؛ بنا براین امکان امکان حرکت آزادانه اسیدها را فراهم می آورد.
برای تائید این نظریه مقادیرPH نمونه های چوب ماسیو نوئل بخار دهی شده و نشده اندازه گیری شد که به ترتیب مقادیر 4.79 و 5.27 بودند؛ مقادیر بالای PH نمونه های آزمایشی بخار دهی شده، این ایده را تقویت و بر آن تاکید می کند .
نتیجه گیری :
از این مطالعه موارد زیر استنتاج می گردد:
1- هم LVL راش و هم نوئل مقادیر دانسیته بالاتری از چوبهای ماسیو همان تنه ها دارا بودند؛ این افزایش نسبی در میانگین مقادیر دانسیته 30% برای راش و به ترتیب 31% و 28% برای نوئل بخاردهی نشده و بخار دهی شده به دست آمد. بعد از آزمون کهنه سازی نیز نتایج مشابهی حاصل شد.
2- میزان مقادیر مقاومت به خمش استاتیک موازی با الیاف نمونه های چوب به میزان کمتری بدست آمد. )6/10% برای نوئل بخار دهی نشده و 25.3% برای نوئل بخاردهی شده؛ نسبت به همانLVL های ساخته شده ازتنه های یکسان). برای مقاومت فشاری نمونه های چوب ماسیو نیز به صورت مشابه مقادیر کمتری بدست آمد. ( به اندازه 6/21% و2/17% به ترتیب برای بخار دهی نشده و بخار دهی شده ها ) ؛ بر عکس مقاومت به ضربه نمونه چوب ماسیو راش24% بیشتر از LVL آن بود .
3- بیشترین کاهش قابل توجه در مقاومت ها به سبب تیمار کهنه سازی، برای مقاومت به ضربه تا حد 25% به دست آمد.
4- فرایند بخار دهی تنه ها برای روکش گیری ، تمامی خصوصیات مقاومتی اندازه گیری شده را به صورت قابل ملاحظه ای کاهش داد؛ کمترین تاثیر روی مقاومت فشاری بود.
5- پانلهای LVL ساخته شده از تنه های یکسان دارای مقاومت فشاری بالاتری از تیرهای ساخته شده از چوب ماسیو بودند . در این مطالعه دمای انتخاب شده برای خشک کردن بر روی مقاومت فشاری پانلهای LVL ساخته شده از نوئل تاثیر مشخصی نداشته است. که البته این امر در مورد تیمار کهنه سازی موضوعیت نداشته است .
6- مقادیر مقاومت خمشی نمونه های LVL از نمونه های چوب ماسیو به صورت واضحی بیشتر بود . در میان نمونه هایLVL نوئل ، بیشترین مقدار مقاومت خمشی برای پانلهای ساخته شده از لایه های هواخشک تنه بخاردهی شده به دست آمد .
7- مقادیر مقاومت به ضربه پانلهای LVL ، بر خلاف مقاومت خمشی وفشاری کمتر از نمونه های چوب ماسیوی که بخاردهی وکهنه سازی نشده بودند است.
Acknowledgment
S. Çolak thanks The Scientific and Technical Research Council of Turkey—Directorate of Human Resources Development for the scholarship during her post doctoral study.
References
[1] T. Llaufenberg, Exposure effects upon performance of laminated veneer lumber and glulam materials,Forest Products Journal 32 (1982) (5), pp. 42–48.
[2] Wang X, Ross RJ, Brashaw BK, Verhey SA, Formsan JW, Ericson JR. Flexural properties of laminated veneer lumber manufactured from ultrasonically rated red maple veneer. Forest Product Laboratory, FPL-RN-0288, 2003.
[3] Hing PS, Paridah MT, Zakiah A. Edgewise bending properties of LVL: effects of veneer thickness and species. In: The proceedings of USM-JIRCAS joint international symposium, lignocellulose-material of the millennium: technology and application, 20–22 March 2001.
[4] Green DW, Evans JW. Flexural properties of structural lumber products after long-term exposure to 150°F and 75% relative humidity. In: The proceedings of 35th international particleboard/composites materials symposium. Washington State University. Washington, USA, 3–5 April 2005, p.3–14.
[5] B.S. Kamala, P. Kumar, R.V. Rao and S.N. Sharma, Performance test of laminated veneer lumber ( LVL)from rubber wood for different physical and mechanical properties, Holz als Roh- und Werkstoff 57 (1999) (2), pp. 114–116. Full Text via CrossRef | View Record in Scopus | Cited By in Scopus (10)
[6] Kollmann FFP, Cote WA. Principles of wood science and technology—I: Solid wood, 1968.
[7] J.A. Santos, Mechanical behaviour of Eucalyptus wood modified by heat, Wood Science and Technology 34(2000), pp. 39–43. Full Text via CrossRef | View Record in Scopus | Cited By in Scopus (20)
[8] N. Yılgör, O. Ünsal and S.N. Kartal, Physical, mechanical, and chemical properties of beech wood, Forest Product Journal 51 (2001) (11–12), pp. 89–93. View Record in Scopus | Cited By in Scopus (14)
[9] J.D. MacLean, Effect of steaming on the strength of wood. A, Wood Preservers’ Association Proceedings 49(1953), pp. 88–112.
[10] Aydın I. Effects of some manufacturing conditions on wettability and bonding of veneers obtained from various wood species. PhD, Thesis, Graduate School of Natural and Applied Sciences, Karadeniz Technical University, Trabzon, 2004 [in Turkish].
[11] I. Aydin and S. Çolak, The changes in some physical and mechanical properties of steamed spruce (Picea orientalis L) wood, Journal of Artvin Forestry Faculty of Kafkas University (2004) [Turkish].
[12] J.Y. Liu and J.D. Mcnatt, Thickness swelling and density variation in aspen flakeboards, Wood Science and Technology 82 (1991), pp. 25–33.
[13] G. Nemli, H. Kırcı and A. Temiz, Influence of impregnating wood particles with mimosa bark extract on some properties of particleboard, Industrial Crops and Products 20 (2004), pp. 339–344. Article | PDF (68 K) |View Record in Scopus | Cited By in Scopus (10)
[14] Carll CG. Review of thickness swell in hardboard siding. General technical report FPL-GTR-96, Department of Agriculture, Forest Service, Forest Product Laboratory, 1996.
Corresponding authors. Tel.: +90 462 377 3244, +90 462 377 3258; fax: +90 462 3257499.
منبع وبلاگ : http://drmb75.blogfa.com/post-9.aspx